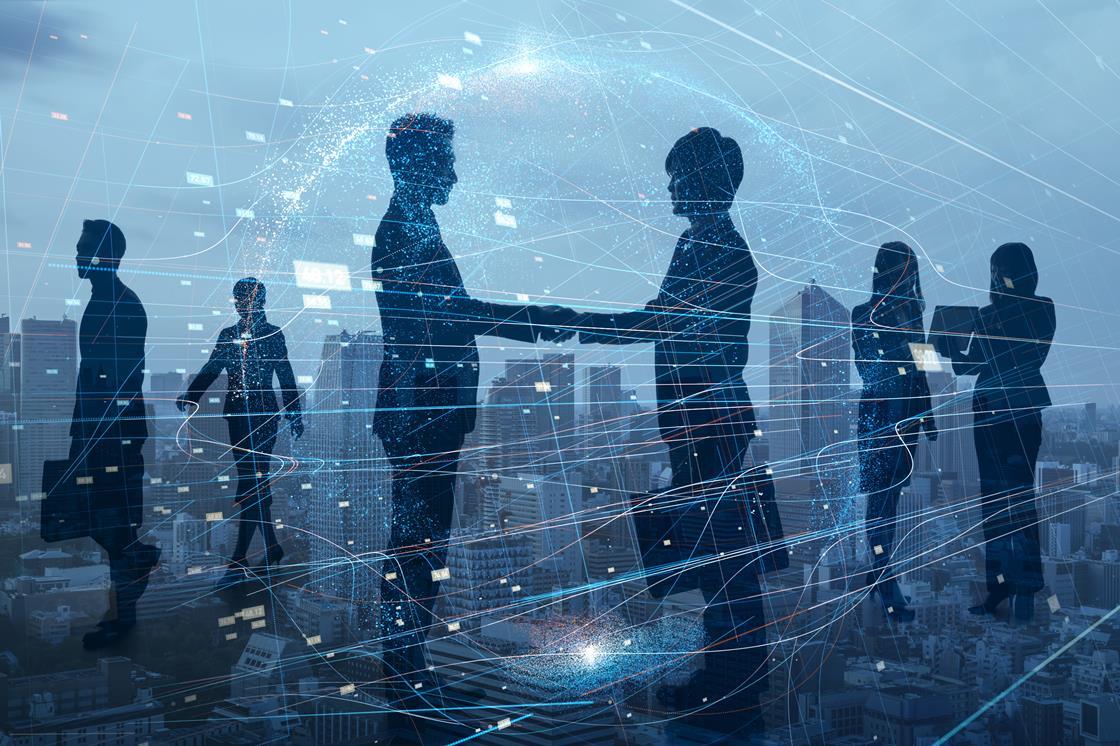
The €1.7m research project, half funded by the Bavarian Ministry of Economic Affairs, hopes the newly developed alloys will be able to serve the safety and weight reduction needs of the aerospace and automotive industries.
Producing the optimum aluminium alloy with a high content of lightweight elements like magnesium through an additive manufacturing process requires a deep understanding of chemistry, thermo- and fluid dynamics.
During the manufacturing process, the metal powder is applied one layer at a time on a build plate and melted using a laser beam. This fuses the metal powder together and forms the desired complex, three-dimensional geometries. The process takes place in a well-defined shielding gas atmosphere.
“Using our proprietary software, which enables big data simulation and analysis, Scoperta-RAD, Oerlikon provides critical solutions for the development of new materials and performance optimisation of available materials,” said Dr. Alper Evigen, Metallurgist at Oerlikon AM.
“There are significant challenges during the additive manufacturing of aluminium alloys because the temperatures reached in the melt pool create an extreme environment that leads to evaporation losses of alloying elements that have comparatively low boiling temperature – such a magnesium,” said Dr. Marcus Giglmaier, Project Manager, AM Institute and Research Funding Manager.
“Additionally, the cooling rate of more than 1 million centigrade per second, create high stresses during the solidification process, which can cause micro cracks in the solid material.”
“Characterising and controlling the gas process during additive manufacturing not only has the potential to prevent evaporation losses, but also to accelerate the entire printing process,” said Thomas Ammann, Expert Addictive Manufacturing at Linde.
“Using a tailor-made gas chemistry for the new alloy would help to control the processes occurring in the melt pool and minimise the compositional changes of the alloys, as well as preventing cracking during printing.”